You’ve heard and can relate to the saying from Gustave Flaubert, “The devil is in the detail.” It refers to the notion that even the simplest of details can be complicated and may cause problems.
As I enjoy continually developing, defining, and refining processes, and talking to other restorers about operations, I found as you adopt a continuous improvement approach to process and clearly defining expectations that it is quite easy to become frustrated by the thousands of details that can easily trip up the most well-developed systems.
Did you ever just wonder or exclaim to yourself, “What in the world! That was a smooth process that has been in place and working for X years!” I am not necessarily referring to a weakness in your operations, a person, or a department although that could be a root cause. I am talking about what could equate to thousands of details daily that are happening in your operation that could be missed even with the best people, processes, and technology in place.
The details may be symptoms of a deeper problem, however. In the context of strong foundations and people, it may simply be a mistake or missed detail. As an example, someone forgot to lock a vehicle or missed the “referred by” in setting up a new job which could result in lost equipment or in the case of the referred by a failure to properly thank the source and comprised reporting. Managing the details is about maintaining your operation and helping talented team members stay great and/or continue to get better.
My unscientific estimate of thousands can be visualized by considering all the details that are happening in each key functional area. For example: administration, sales, production, project management, accounting, and human resources. I did not do a formal count as I lost track somewhere in the hundreds and decided to go with thousands. The following is a rambling list of detailed related activities and/or information. The reality is that the exact number is irrelevant, managing them all proactively versus reactively is what is important.
- Job related information and data, file updates, pictures, contracts, videos
- Estimates, change orders, invoices, collections
- Ongoing communications, how to communicate, when to communicate, and how to document communication
- Training, development, human resources
- Safety, PPE, compliance
- Inventories of supplies, PPE, equipment, batteries, uniforms, etc.
- Vehicles and equipment, cleanliness, repairs, maintenance
- Accounting, bills, receipts, job costing, payroll
- Sales and marketing
- Warehouse and facilities, organized, clean, efficient design
- We did not even get to field execution and production: floor protection, quality, schedule, subcontractors, contents processing, lots of details.
Being paralyzed or frustrated by the details that could be compromised or allowing them to spiral into complete breakdowns of your well-established systems, processes, etc., is not an option. The following is a brief list of tips to manage the details so you can focus efforts on the development and implementation of progress, growth, and other high impact initiatives. The following is based on starting with a solid foundation that includes a healthy culture, engaged team, relationships built on trust, and good team morale complete with positive recognition and reinforcement. A team with leaders that buy into the concept of constructive feedback for continuous improvement will be impacted in a positive way by the following tips:
- Tacit Approval: Avoid ignoring the problem of the missed detail. This could spiral quickly into a bigger process breakdown. You can learn more about tacit approval in the following Restoring Success. The management theory of “things that get noticed get done” applies to this tactic.
- Software Systems and Reporting: Utilizing software to monitor, manage, and report some of the details will help efficiently identify a variety of blips. Once you are using technology to do this, reviewing the information, and addressing any of the details that are out of compliance must be a clearly defined responsibility in your organization and must be consistently done on a schedule or in a timely manner.
- Inspecting: In addition to using digital tools/software, developed visual inspections, checklists/forms, and a schedule can help keep the details in check. This approach is effective in evaluating field work, job site safety, warehouse, and vehicles. Inspecting our own work and as part of our SOPs also helps to proactively manage the details and minimizing misses.
-
Systems by Design: Developed systems that support detail success and support inspections will serve the team well. A few examples to illustrate the concept:
- The company process may be that the vacuums are put into their designated location at the end of every day. They should be clean and field ready. If there is a designated location and it is labeled, a quick walk through of the warehouse at end of day (or beginning of next day) will allow for a quick visual inspection as a missing vacuum will be evident.
- In a vehicle a shelf is labeled five extension cord reals, it is extremely easy upon inspecting and evaluating if there are in fact five, an important detail.
- Responsibility: Clearly defined roles of who is responsible for the outcomes, oversight and, addressing details is integral part of keeping the details in check.
- Speed: Addressing details cannot wait 6 months or when we get to it. When addressed quickly, we better prevent the compromised detail from recurring. The timeliness of addressing the detail is the right thing to do for the team member’s individual success. Imagine waiting for an annual review or waiting till the detail has escalated and sitting down with someone saying, “We have a severe problem. You have not been locking your vehicle for 6 months.” And the response is, “I am sorry. Why didn’t someone tell me?” (A dramatization for illustration purposes)
- Retraining: Retraining helps solidify details and keep them top of mind. Some of the courses that we have developed I believe are important in the retraining category to help proactively manage details and include but are not limited to: Job Site Behaviors and PPE with a review of proper donning and doffing. You can gain free access HERE.
- Tools: As a team, brainstorm, and develop tools and approaches to managing the details proactively and constructively. The following is an example of a tool for leadership to address details quickly and positively, Inspiration Notes:
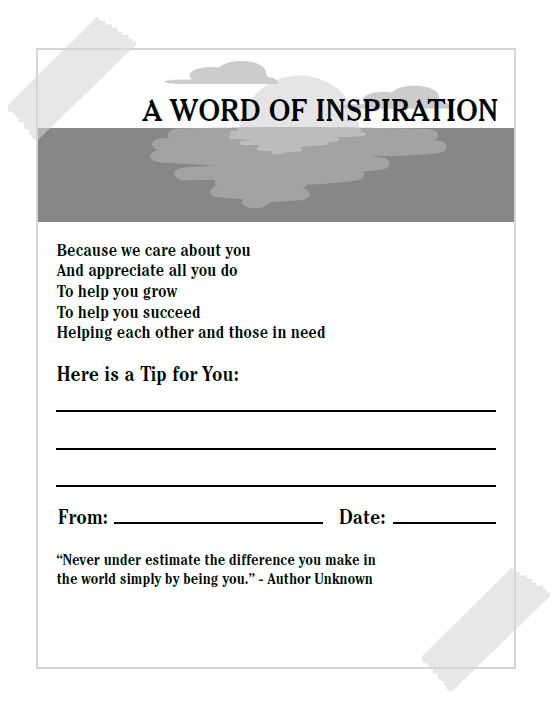
Do not let blips in the potentially thousands of details that make your company great get you frustrated, or fester. Each detail typically has a chain reaction impacting other areas, details, customers, and people in the company. Make open and constructive feedback part of your healthy culture, keep the details in check and spend your energy on positive high-impact initiatives by having a proactive approach to managing all the details that matter.
Happy Restoring Success and Managing Details.
Report Abusive Comment