The R&R 2016 Case Study Contest is on! Read through each case study, then click on the Cast Your Vote link to vote! Finalists will be featured in the June issue of R&R.
Project #1: McPhee Home Insect Infestation
Company: Noble Pine Products, Mount Vernon, NY
The Job: Customer called about unknown insects biting her and her family.
The Challenges: We had to try and identify the insect based upon her description, without photos, and to determine whether or not our product, Sterifab, would have efficacy on this insect, and recommend treatment. The main hurdle was trying to evaluate her information over several phone calls. Many "infestees" suffer from delusional parasitosis, and quite possibly could be imagining a big part of the problem if not all of it.
The Solution: After listening to her description of the rash and marks, and combing through scores of pictures of bites and rashes, we were pretty certain that her house was infested with dust mites. You have to rely on marks since you can't see dust mites, and what people think are physical bites, are the allergic reactions. We recommended several national pest control companies, and suggested to have them call us after they had assessed her property. The Pest Control Operator called us and affirmed that the problem was indeed dust mites.
His team thoroughly cleaned and vacuumed the home, threw out old bedding and pillows, and recommended removal of old rugs and replacement of blankets and sheets. The subject apparently agreed to his suggestions.
After all remediation recommendations were followed to the letter, the exterminator returned and sprayed Sterifab on all surfaces within the house. Now, with some five months after treatment, the McPhee Family is back at home, bug and itch free and living large!
Project #2: 165 Hotel Rooms with Water Damage
Company: Kowalski Construction, Inc., Phoenix, AZ
The Job: Late on a Saturday, we received a request for water damage emergency services as a result of a large storm. The initial reports indicated approximately 125 guest rooms on 4 floors, business center, meeting facility and storage rooms were damaged. Water was coming in from the roof and had impacted all 4 floors. Crews were immediately deployed and work began right away and continued around the clock to mitigate the damages.
The total cost for the emergency services and restoration was $976,209.
The Challenges: The hotel did not have anywhere near enough vacant rooms to relocate the affected guests and closing was not an option so work was coordinated to create the least impact possible on existing operations as well as on the guests. The facility did not have a service elevator and only two guest elevators which created a challenge for moving all the equipment, material and personnel in and out. We removed windows from the building in order to expedite debris removal and had to protect the landscaping and guests from harm.
We immediately removed all of the textiles in the affected rooms, had them cleaned and stored off site, bringing them back as the rooms were completed.
Demolition was required so we had to arrange for hazardous materials testing to begin immediately. We were able to get a testing laboratory to open on Sunday around midnight to provide us the results right away. With the clearance in hand, the demolition process began which uncovered multiple ceilings. The finished ceiling was drywall, with an acoustic grid ceiling above it and yet another drywall ceiling above that. We had to arrange for the testing to begin immediately on the now visible ceilings and get the laboratory to open up after hours once more.
The amount of equipment needed to dry this job required more electricity than the hotel had available so we brought in a 250 KVW 120/208 3 Phase trailer mounted generator, ran lines and distribution boxes to power our drying equipment.
The original report identified all of the damaged units on the south side of the building, except for 1. Inspection of the surrounding rooms seemed to indicate the damage was isolated to this one unit. Two days later, they identified additional damaged units on the North side of the building on 3 floors.
During the course of the project there were 3 more water intrusions since the hotel hadn’t arranged for corrective repairs yet.
The amount of water in the structure now required for more drastic measures. We decided to bring in 3- 5,500 CFM and 1- 6,000 CFM – Tractor Trailer mounted desiccant units. Two of these units were fueled by propane which were overheating in our August, Phoenix heat. To combat this, we brought in 2 – 10 Ton Portable A/C units to cool them down.
Refueling all our equipment with diesel became a job in of itself. We were bringing in 242 gallons a day to run the equipment and on several occasions had to make additional trips for even more fuel.
Once demolition was completed, we discovered some structural steel that had been compromised over time and worked with the city building department and an engineer to affect repairs. Additionally, the city inspector required fire taping which we performed. The fire protection system failed due to the storms requiring a round the clock fire watch until the system could come back online. This prompted an inspection from the Fire Marshall who determined that the measures we put in place were more than adequate along with his history with our company; he didn’t require any further inspections on his part. We received a surprise inspection from the county air quality department who found everything in order and allowed us to continue with our progress.
With all the equipment on site, power cabling and liability potential, we maintained 5 full time police/security officers around the clock.
During all of the work, we had to maintain a clean and functional environment for the hotel guest and staff. We kept the floors protected, power washed walkways and parking lot with a trailer mounted pump twice per week to maintain a welcoming appearance for new guests.
The Solution: The hotel is a part of a chain and customer satisfaction was monitored continuously during the mitigation and restoration process. They were able to maintain satisfactory scores which were critical to them even though corporate didn’t take their current condition into consideration.
With the tremendous amount of equipment and supplies on site at all hours of the day and night, no theft or items were reported missing. Even with all the dangerous conditions, no injuries were reported.
We were able to react quickly to the changing conditions of the additional storms, uncovered damages, failed fire protection system, city building department’s requirements and still keep the project on schedule.
We worked on a total of 165 guest rooms on 4 floors, business center, 200-person meeting facility and storage rooms. The scope of the work was constantly changing and being adjusted to. The project was fully restored and did not close a t any time due to the loss.
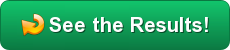
Report Abusive Comment