Paul Davis Restoration recently completed a major mold remediation of a sport arena on the campus of a Big Ten university. Carlos Martinez, project coordinator, and Hugo Rivas, project manager, answered some questions about the project.
R&R: What was the incident that created the need for the project?
Martinez: Flash floods outside of the arena pushed through the seals of the exterior doors closest to the gym floor. The contractor that has handled mitigation services in the past for this facility told them they were unavailable. We jumped at the opportunity and walked the loss same day.
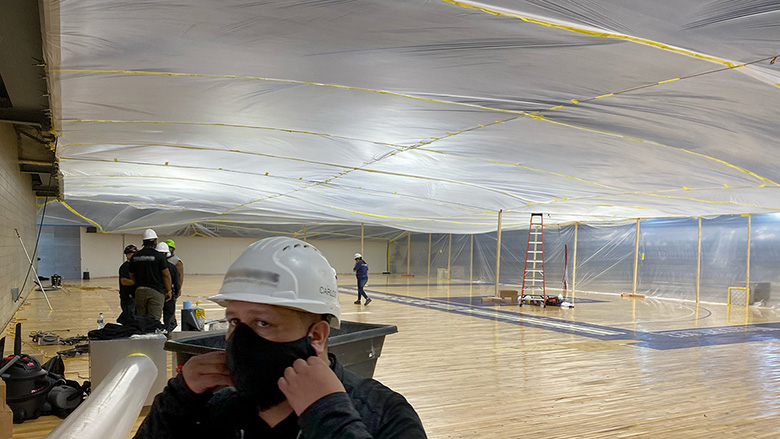
R&R: What did the project entail? What was its scope?
Martinez: There was a delay due to figuring out coverage between the general contractor which recently completed renovations of the affected area and the insurance carrier. This delay created an opportunity for microbial growth which changed our initial scope. Our scope was to mitigate water damage in the nearby locker room. We removed the vinyl base, removed wet drywall and insulation from insulated walls, applied anti-microbial and set drying equipment. In the arena our goal was to remove the affected flooring system and to remediate microbial growth per the IH protocol.
R&R: What unique or major challenges did you face from this project? How did you resolve them?
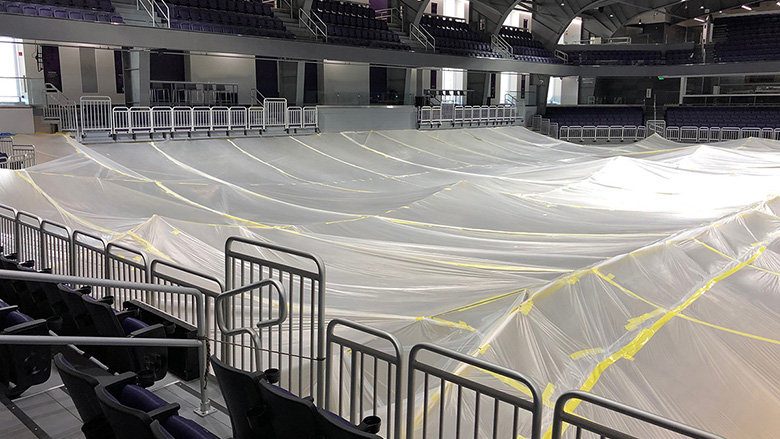
Martinez: Creating a drying chamber in the arena was our biggest challenge. Our veteran project manager, Hugo Rivas, designed the most effective containment that I have ever seen. A combination of 2x4’s, poly sheeting, tape and parachute cord. This containment also had filtered penetrations to allow airflow when negative air was needed.
Another challenge was time. We had less than two weeks to complete the project. In order to meet the deadline, our twenty-person team worked long days. Also, our drying methods using multiple forms of dehumidification were key to our success.
R&R: How did you handle communication during the project?
Rivas: For the duration of the project, we held daily meetings at 11am. Invited to these meetings were the Paul Davis project coordinator and project manager, the arena risk manager, and the facilities director. Also invited to the daily update meeting was the insurance adjuster and industrial hygienist. During this meeting, we discussed daily moisture readings, status of the demolition, and the executive summary from the previous evening. At the end of every work day we sent an Executive Summary that included how many personnel were on-site, work completed, tasks in progress, and a moving forward section with tasks to be scheduled.
R&R: Did you learn anything that you will use in the future?
Rivas: The containment built also acted as a dust and debris barrier. This not only allowed us to mitigate the water damage faster, but also protected the rest of the arena from contamination. Saving the carrier and insured time and money.