The indoor environment is an inherently complex system. There’s the building itself, of course. The design, materials, systems, and so much more come together to create a home, office, retail space, hospital, school, and so on. Then, the occupants bring in all their things. As they settle in, their activities come into play as well. Also contributing is the way the building is operated – temperature and humidity settings, ventilation, and maintenance, to name just a few.
So, what happens when something goes wrong – when there’s a flood, fire, or structural damage? That’s where the remediation and restoration processes come in. Damaged materials are removed, replacement materials are put in place, cleaning is performed, and the space is restored to pre-damage condition. That’s the ideal outcome. It seems pretty straight-forward, but you’ve likely experienced your fair share of projects where it wasn’t quite that simple.
So, how do things go sideways? With such a complex system, it’s inevitable that unintended consequences will occur. These could range from unpleasant odors to negative health effects to secondary issues to something completely unexpected. How these consequences are addressed makes all the difference between a satisfied customer and an unhappy one.
Unpleasant Odors
This is probably the most common problem, and it may have nothing to do with the quality of your work. Odors occur in an array of different situations.
It may be nothing more than new materials off-gassing at a high rate. All new materials off-gas, meaning chemicals from the manufacturing and/or packaging process are emitted from the surface of the material. New materials have been minimally exposed to air, so the surface is “fresh.” Think of a piece of pine 2x4 that’s been sitting around for a year; it doesn’t have much odor, but if you cut off the end suddenly the pine smell is much stronger. This is what is happening with all the new materials in the building (and many of the older materials as well) and the additive effect can be overwhelming, especially if the ventilation is minimal.
Interactions among materials, activities, or conditions are also quite common. For example, let’s say the remediation included replacement and subsequent painting of a large section of drywall. There’s a strong odor and ozone generators are brought in to get rid of that odor, however, after the treatment there is a different but still unpleasant odor. Ozone can affect the structure of the paint itself, breaking the bonds that bind the paint together. It won’t look any different but the smaller chemicals that are generated by this process, typically an array of acids and aldehydes, cause a really unpleasant odor. This is sometimes referred to as “sour paint.” Unfortunately, there’s very little that can be done to address this problem. Sealers are helpful but may not be sufficient to prevent the odor from leaking through light fixtures and electrical sockets from the back side of the drywall.
A similar situation occurs with spray foam insulation when the temperature, mixture proportion, flow rate, thickness, or light exposure are outside acceptable parameters. The resulting applied spray foam does not cure properly and often leads to significant odor or health problems. It’s not really feasible to effectively seal spray foam insulation so complete removal is the only option, and since it’s not meant to come out this can be a challenging undertaking.
Negative Health Effects
These can be devastating and sometimes exceptionally difficult to track down, especially if the symptoms are mild at first. I won’t go into a lot of detail regarding possible symptoms; almost any symptom or condition can arise from or be exacerbated by poor indoor environmental quality.
There may simply be too much in the air for the body to handle, this is referred to as the toxic body burden. Again, new materials will add significantly to what’s in the air. And sometimes it’s less the amount than the composition. We’re all familiar with formaldehyde which is present in all wood materials and is especially high in any products with formaldehyde-containing resins. When you add wood flooring, furniture and the wood contained in the building itself it can amount to quite a bit.
Adhesives can be pretty potent as well, especially those containing aromatic or chlorinated solvents. Paints and other coatings are another substantial source. As a side note, low and no-VOC coatings still contain VOCs; there is a technical definition of a VOC that allows for use of “exempt” VOCs in place of more traditional hydrocarbon mixtures.
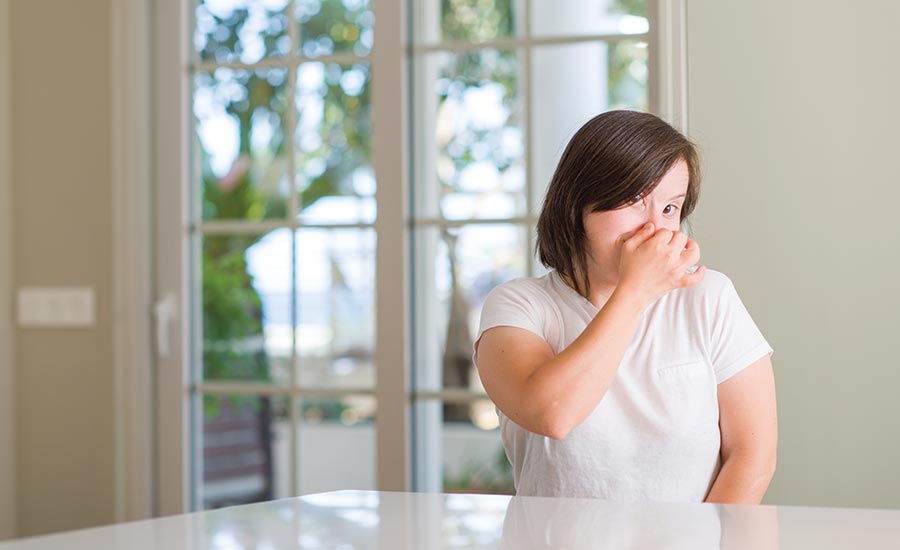
Secondary Issues
Secondary issues or effects can be a bit harder to pin down. One of the largest is the ventilation configuration. Whether mechanical (open windows) or a forced air system, the amount of outside “fresh” air will have a major effect on the indoor environment. A very tight building with minimal air turnover that uses the lowest emitting materials possible will likely still have a sizable indoor air problem while a looser building that has higher emitting materials may actually have better indoor air quality.
Another aspect is the general condition or maintenance of the building. The problem area may have been properly remediated but if there are other problems it may appear that the work was incomplete or ineffective.
Every project brings its own unique circumstances and challenges. Having a good understanding of how the various pieces interact will go a long way toward addressing the inevitable problems quickly and effectively.
Report Abusive Comment