Take a moment to answer a few questions. How long do you think it takes to fully dry a structure? Do you believe you can do it in only three days? Does it just take longer? This topic has been plaguing restoration contractors for years. Now, it’s time to put the argument to rest once and for all, with the help of three drying experts.
Give us a little background on your industry involvement, specifically as it relates to drying.
Ken Larsen
This year marks my 40th anniversary in the restorative drying profession, half of which I practiced as an independent restoration contractor. The remaining half I have taught IICRC and ACAC water damage related courses and proudly provide tuition for the industry’s capstone designations: RIA Certified Restorer (CR) and Water Loss Specialist (WLS) courses. As founder of the Registered Third Party Evaluator (RTPE), we provide independent and unbiased consulting on restoration projects. I also provide expert witness services and am the author of the industry’s most authoritative technical manual on the subject of structural restorative drying, Leadership in Restorative Drying – Gold Edition.
Kris Rzesnoski
Currently, I am the VP of Business Development and the technical consultant within Encircle for development of our field documentation, drying, and contents software. With over 15 years in the insurance and restoration industry, I have had the opportunity to work with many companies and run large operations. I have successfully completed the Masters of Fire & Smoke Restorer, Master Textile Cleaner, and Master Water Restorer courses. I was also able to join the ranks of some very distinguished restorers by obtaining the Restoration Industry Association’s highest designations of Certified Restorer - #657 and Water Loss Specialist - #169.
R. David Sweet
While my professional career began in corporate finance, my father often asked me to help with a couple of his files as an independent adjuster. Soon, I became an IA myself, and after about five years in, I saw the opportunity to start my own restoration company. For the last 19 years I have run a full-service restoration company. In that time, I became a double master with the IICRC, acquired five ACAC professional designations, became a Florida State Certified General Contractor, Licensed Microbial Remediator and Assessor, WLS recipient with the RIA, and Charter RTPE with IDSO. The changing climate in Florida’s insurance claims processing has provided the opportunity to be an expert witness on mitigation, fire, remediation, pricing, and more.
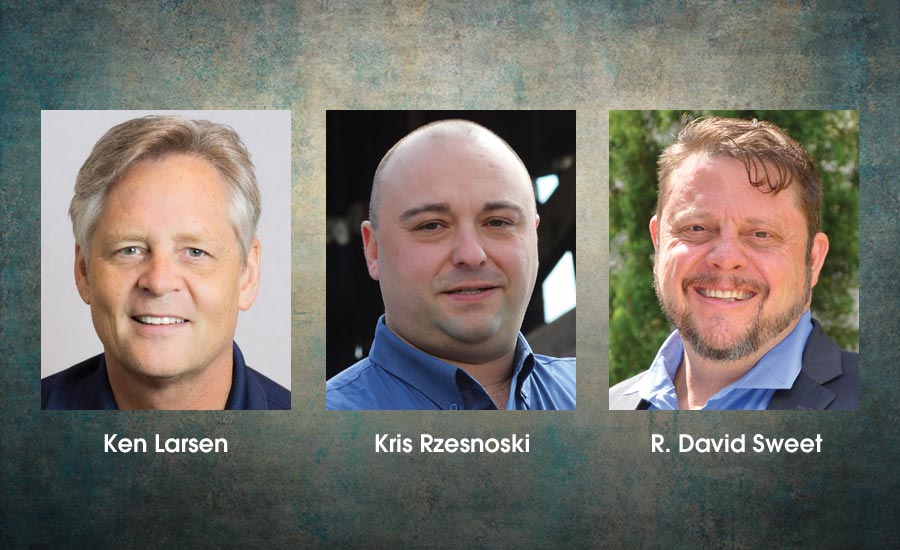
Do you believe a structure can be dried in three days? Why or why not?
Larsen: The operative word here is “can.” Certainly, some building materials in some scenarios – CAN – be responsibly dried in three days. The problem occurs (or happens, or starts) when someone utters over-generalized statements like, “drying structures takes only three days.” Another position often leads many to assume that structures requiring more than three days to dry will require approval from the claims representative. Different materials will absorb and desorb moisture at different rates – and this is governed by the laws of physics. It is not governed by an individual sitting behind a desk who “grants approval” for the extended time dictated by physics. While some may not like to hear it, it is not uncommon for structural drying projects to take the better part of a week, and in some cases even weeks, to be competently and adequately dried.
Rzesnoski: The true answer is that it depends. For the most part, three-day drying does not fully achieve your drying goals. We see many restorers not considering the stabilization process as a separate process to drying the structure. Stabilization is preventing the humidity in the structure from rising while coverage or hazardous assessments can take place. When drying commences, you are then left with saturated materials that take additional time to dry. What we see in most drying scenarios today is that the proper amount of equipment is not being deployed for a number of reasons: the insurance company wants the occupants to remain on site, there is not enough power on site, temperatures have to be controlled so the occupants are comfortable and therefore, some equipment is turned off prematurely, etc. All these factors go against the restorer’s efforts. Today, many more skilled restorers are taking longer to dry structures due to the fact that they are doing a proper moisture map of all affected materials.
Sweet: While I believe particular materials in a structure can be returned to dry standard in three days (carpet, cushion, trim, and perhaps drywall), the actual structural assemblies are more often omitted from inspection techniques (framing, floor assemblies, concrete, etc.) as they cannot. So, if your definition of “dried” is flexible enough to be limited to the surfaces you see and feel, then the answer is yes. If you are a little less flexible in your practice and believe that ALL the materials in the structure should be returned to their pre-loss/dry standard moisture contents, then typically, the drying curve will not show the WHOLE structure as returned to dry standard in three days.
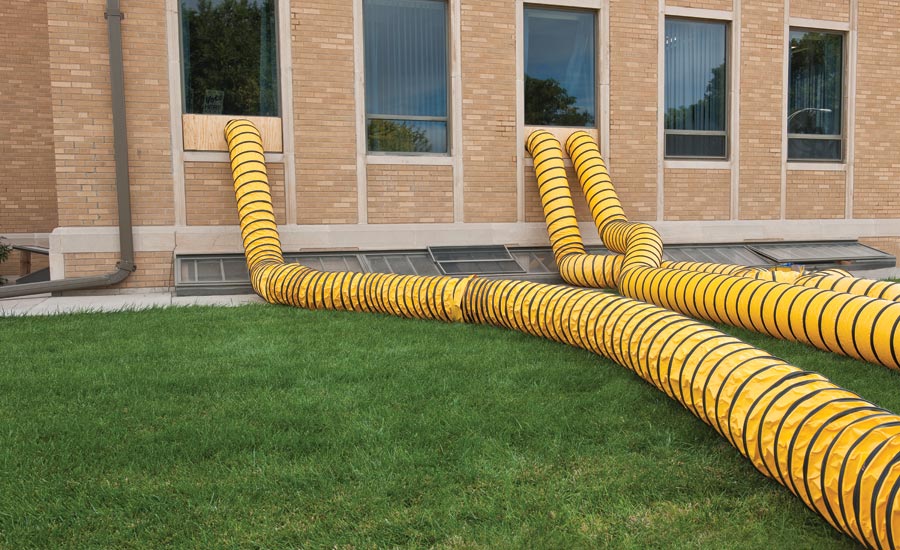
How can a contractor know for certain if a structure is returned to acceptable moisture content? (a.k.a. acceptable “dryness”)
Larsen: Many will argue that as long as the material/atmosphere will not support mold growth, (def. “secondary damage”) the material is adequately dried. This is a grave error. Competent restoration is rarely to return the structure to a “damp, but not damp enough to support mold growth” condition. The contractor must warranty the structure for workmanship – and issues like paint failure, nail-pops in gypsum, trim work quality, squeaking floorboards, etc. are but a few issues that can appear as the structural moisture content changes from damp to normal. Restorers must account for both dimensional changes as well as manage microbial risks.
Rzesnoski: You know the structure is truly dry when you reach the dry standard of that building. However, that is easier said than done. In my experience, you need to follow a systematic approach to testing and validating your materials in the field and gather that information. What I see happening today is that the downloaded pressures of the carriers and TPAs are creating barriers to properly conduct the work in the field. When the contractor is told they will only get paid to have equipment on a job for a specified limit of three or four days, it creates unrealistic expectations on the restorer to perform with limited time and payment. Couple that with a contractor that does not properly size the equipment needs for the job and you are running into a dangerous situation.
Sweet: The only way that a contractor can know for certain that a structure is “dry” is to follow these steps:
- Find the dry standard value for each assembly/material type.
- Completely moisture map ALL building assemblies/types to find what is elevated.
- Have the courage to dry the structure, without compromise – regardless of the cost, documenting not only what you did, but the science that supports the “why.”
I know many people cringe at the thought of explaining extended drying cycles and larger loss severity. I also understand relationships and business. I’m talking about our integrity and character; there should never be a price tag on that nor any relationship that we feel obligated to give it up for. If we cannot be trusted to be advocates for truth and standards, we have become irrelevant to the industry and devalued as professionals.
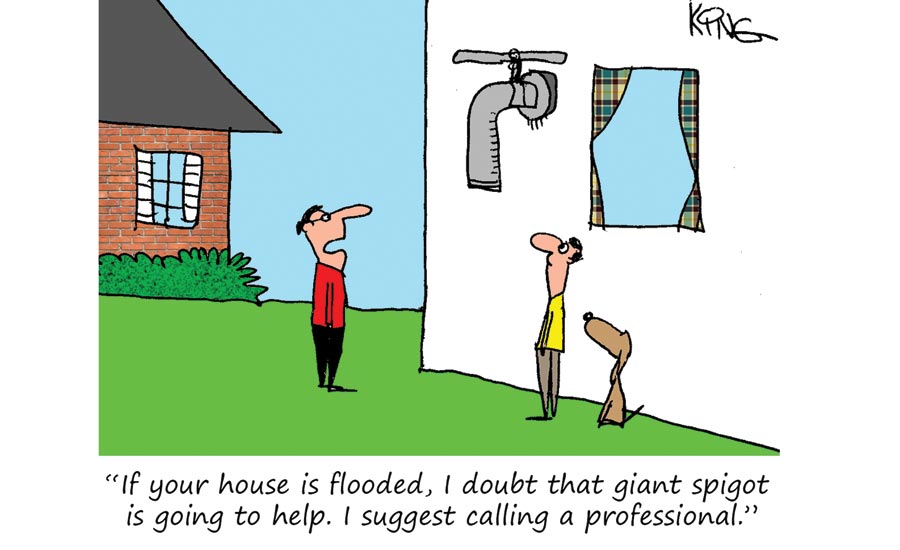
What kind of documentation should contractors embrace to record their drying process, dry time, equipment usage, and so on?
To answer this, we can look at the mold remediation industry. Why do most mold remediation services involve a qualified, independent, third-party mold consultant to evaluate and document the mold remediation efforts on their projects? The answer is obvious:
- The contractor possesses a clear conflict of interest if they collect their own data. It is incredibly easy to manipulate the tests to produce the data they desire, andunderstandably, the insurers and consumers do not trust data if collected by the contractors.
- There is risk associated with collecting data used to justify your own workmanship. It is always nice to “share risk” – especially if you can share it with someone very qualified.
Insurers and TPAs insist upon drying records from contractors, yet fail to adequately compensate the contractor for industry standard quality documentation, understand how to competently interpret them, or use the records against the contractor rather than in support of their processes. Therefore, I recommend contractors simply remove the drying documentation services from their offerings. Tell them you no longer offer that service. (More on this in question 6.)
Rzesnoski: This is the worst part of any technician’s job... doing paperwork. It starts with proper documentation at the beginning of the claim. Identify the cause of loss and make sure it is not going to impact your drying plan. Size the job for the proper starting point of equipment, both dehumidification and air movement, and adjust the equipment as the needs of the structure demands. This means knowing where you are trying to get to and how you can change the atmosphere and equipment placement to reach your goals. If you are not on a digital system that allows you to take your readings in the field so that your office knows what is going on, you are behind the curve.
Sweet: The S500 and S520 give us excellent starting points. While we can’t cover it all specifically in this article, here are some reference points:
- S500 - 1.2.2
- S500 - 1.2.2.1 Moisture Detection Equipment
- 1.2.2.3 Final Inspection (Completion)
- 1
- 9.2.3 Project Monitoring Logs
- 9.2.4 Required Documentation
What are the risks if a structure is not dried properly?
Larsen: See question 3.
Rzesnoski: Do you say it? MOLD! The black stuff can impact your reputation in your market, and with social media where it is today, you can go from a successful obscure shop doing good things to being painted as the mold monster! If you haven’t learned yet, as the restorer, you own the risk - wait and see. The same programs that push down three day drying will hold you accountable for not properly drying out the structure. When you succeed they reap the profits! When you fail, you fail alone!
Sweet: Consider this for a moment. One small child become sensitized to Endotoxins, Exotoxins, Mycotoxins, VOCs, And/or other toxigenic/allergenic components that are the undeniable results of incompletely dried structures. Calculate the staggering expense of a lifetime of doctor visits, medical care, and just over-the-counter medications alone. Now, consider what the effects from all of the missed schooldays and work will have on the career trajectory, and even what is available as careers, to medically challenged individuals. The emotional costs of frequent sicknesses and the general lack of wellness someone subjected to these conditions might experience – FOR A LIFETIME – is too much. Consider the human toll.
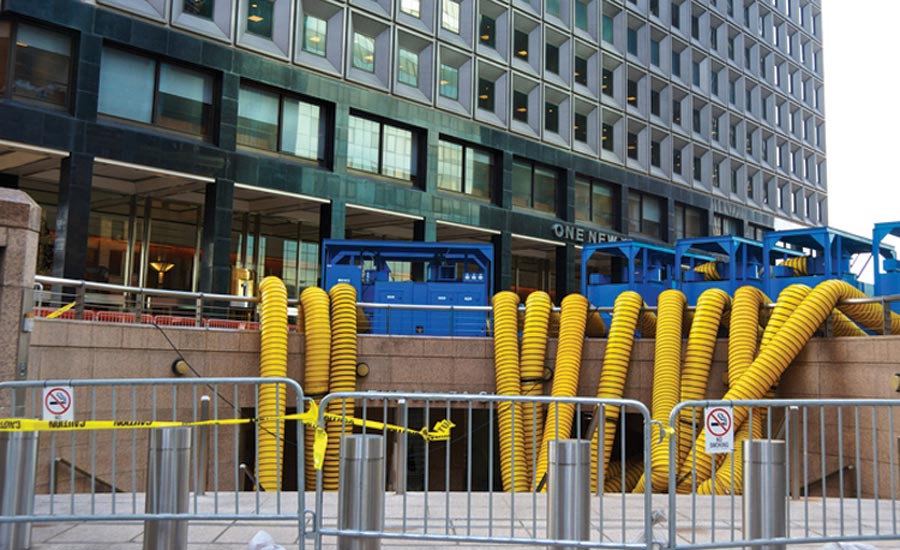
What are your thoughts on stabilization vs. restorative drying? Why do we not see more of this?
Larsen: We [RTPEs] see a two-part distinction between mitigation phases all the time. Just like a quality mold consultant who guides competent mold remediators, an expert third-party restoration consultant can guide restoration contractors in their restoration protocols; complete with both phases of mitigation (stabilization vs. drying). To be honest – I am unsure how any contractor can competently execute a Category 2 or 3 restoration strategy in the absence of segregating their mitigation into two phases.
Rzesnoski: See question 2.
Sweet: If this is not a hot topic where you are, it will become a very contentious discussion shortly. The carrier is in a real pickle here. They have a policy that both requires immediate action to mitigate loss AND includes the “right to inspect.” Right to inspect is a very polite way to say, “You WILL allow us to inspect the property, and as often as we wish.” Carriers want us to move fast to mitigate, but not TOO fast. They want to move the loss forward but without sacrificing any control their contracts provide to them. It can feel a little like a darned if you do, darned if you don’t environment, but a contractor is exposed (along with the client) either way. In my personal practice, we stabilize. I would rather explain that my actions served the requirements of the contract than expose all parties to a possible denial. This places the requirement on the insurer to be professionally prompt and make a decision and protects our clients to the extent we are able.
What can contractors do when an adjuster or carrier doesn’t want to pay for additional drying time?
Larsen: Short answer: talk to an attorney. Longer answer: avoid the situation all together by bringing in an expert at the START of every job. Seriously. It’s expensive and difficult to bring in the expert after the job is done and the decisions have been made. On the other hand, when the adjuster or carrier knows they must argue with a third-party expert about the job, they have a far greater hill to climb.
Rzesnoski: This still comes down to a business decision you need to consciously make. It’s to sit on the sidelines and tell people what to do, but until you have experience running the show and being responsible for the financial fall-out of making a bad decision or series of blind decisions, you have to take control. If you decide to do the work, do it right. Your reputation is what is going to keep you in business and maybe you are at a point in your business where you need that work. If you are, document everything and protect yourself. Your profits may be reduced, your liability may be increased, but if that is what you need to do make it a conscious decision.
Sweet: DATA, DATA, DATA – Nothing confronts what people think more than FACTS – which eventually, they must accept. The beautiful thing about data is that there is no way to explain it away. Take the opportunity to show whoever is asking what a great job you did, why you did it that way, and the fact that you reconciled your billing before it ever went to them. Don’t be a troll – Be polite – while you build a relationship based on truth.