You should know what I believe before reading this article. I believe that carriers and contractors can work well together if their relationship is built on trust and a mutually accepted goal to reduce costs, both be profitable, and to provide exceptional customer service.
I have changed my view on the industry in the past few years. I am not anti-carrier/third party administrators, but I am not pro-carrier/third party administrators either. I tend to lean to be pro-contractor, but only because the value of a good contractor can help a carrier be more profitable. That also doesn’t mean I will stand behind all contractors, because there are enough out there to warrant a carrier to question their quality, billing, and business practices. I don’t share the premise that if you write a number on a paper you are entitled to the compensation unless the work you did warrants payment.
My bias creates my mindset that the carriers have to protect their purse strings due to the fact that the misinformation of many uninformed contractors have lead the good contractors to get pulled into the cyclone of shh … Category 3 water.
Ken Larsen wrote a rebuttal back in the April 2009 issue of Property Casualty 360 to an article to an article stating inferior contractors would take more than three days to dry. If you don’t know Ken, you should acquaint yourself with him and his book “Leadership in Restorative Drying.” Not only has he taught IICRC courses and is one of the instructors of the Restoration Industry Association’s top restoration designation the Certified Restorer, he also created and now sits as a Register Third Party Evaluator who reviews jobs as an independent third party to help carriers and contractors validate the work being completed. To say he is an authority in restorative practices would be an understatement.
Recently, I asked Ken to revisit this article with me and keep the discussion going 10 years later. I wanted to talk from a competent restorer position and examine how today’s science, technology, and drying theories hold up to the three day drying myth? The goal of this article is to lay out the facts of the restoration industry to help build the bridge between restorers and their clients.
I was inspired to write this back in November 2016 when I was talking to the VP of Claims for a leading Canadian insurer who advised me that he thought some of his best contractors were incompetent and were drying jobs in seven to 10 days. Frustrated by their delays, he refused to pay for these “outrageous” drying times. He asked me the question “Why take seven to 10 days to dry, when three to four is all a competent company needs?” This lead to a 15 minute conversation/rant about why I would choose those guys over the others. I stated that in today’s environment if you have a contractor who is confident enough to justify their need for more time and equipment rental and are willing to go against the industry grain, you should listen to what they have to say. At the end of the day, I would have more confidence that those contractors are the ones saving the carrier more money than following the three or four day program.
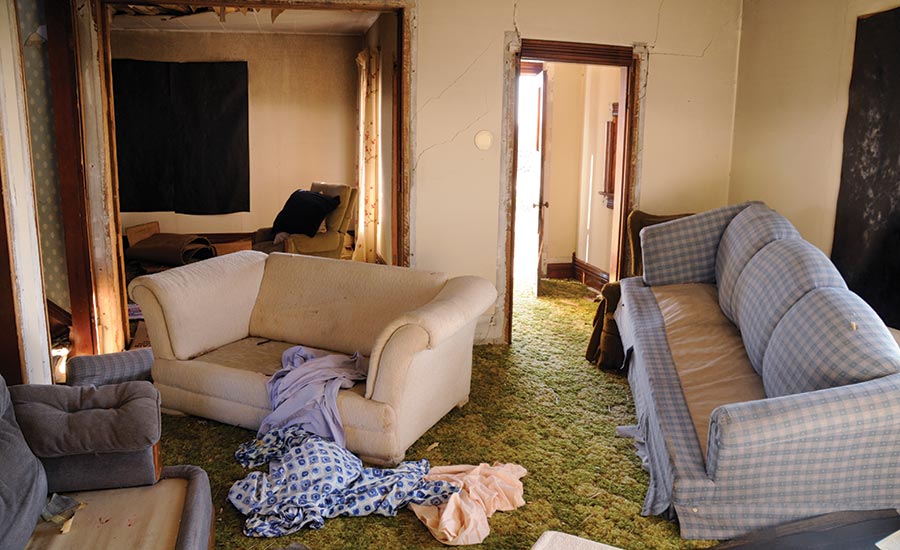
The 2009 Myth
In the 1990s and early 2000s, restorative drying science was in its infancy but was evolving as some thought leaders in the industry began taking a more scientific approach. Restorers were rapidly moving from being carpet cleaners to restoration specialists, and in the process, they were learning what worked and what did not work. Those restorers worked to understand the science that impacted their business and developed the technology still used today.
As restorer confidence began to grow, the training of restorers needed to grow as well. The term Applied Structural Drying (ASD) became known in the industry as a drying course. The Institute of Inspection, Cleaning and Restoration Certification (IICRC) stated in its IICRC S500 V3-2006 standard, “Currently, among the IICRC’s 38,000 registered technicians, approximately 24,000 are IICRC-certified as Water Restoration Technicians (WRT), with approximately 4,500 of those being certified in Applied Structural Drying (ASD). This number is growing daily. ASD is primarily a hands-on course in which demonstration houses representative of standard residential construction are flooded, extracted, monitored, and dried throughout the three-day course – although three-day drying cannot be guaranteed.”
Everyone was going to these classes, from contractors to adjusters to property managers. The fact that a restorer could reduce the cost of rebuilding a structure substantially impacted the bottom line of the final customer, reduced cycle time, and decreased rebuild costs.
The issue with these classes was that they consisted of a three-day class. The perception was that structures could be dried in three days. The reality is that many of these structures remained wet for three to four days after the class ended.
The untold truth was that even with a sanitary environment with limited contents, more than enough power and with known quantities, known saturation times, and a repeatable process, these buildings still required additional days to dry.
Some contractors and adjusters believe contractors are in possession of technology, equipment, and training that can dry structures in three days. In 2009, Ken wrote: “They (insurers) may even accuse contractors of being unscrupulous and advise adjusters to alter the contractor’s invoices based on wishful, non-existent quotations. The fact remains that these sceptics are hard pressed to substantiate their comments. Moreover, publishing erroneous materials can lead to serious conflicts between contractors and adjusters rather than assist in fair and scientifically sound practices.”
Drying Science in 2019
In 2019, the science has evolved, the equipment has evolved, and restorative techniques have dramatically improved. But with all this improvement and knowledge one thing is true – three-day drying is not the norm. Stephanie Beattie of the Center for Disaster Recovery in Barrier, Ontario stated the best statistics show we went from an average of 6.2 days in 2016 to 4.9 day in 2018.
There has been plenty of research by the restoration (restorers) community and building science (engineers) community to substantiate the fact that not all materials can be dried in a specified, arbitrary time of three days. As a matter of fact, many structural materials will dry in varying degrees, depending on saturation time, atmospheric conditions and the material’s location in the building composition.
Ken had predicted the pressure on pricing would motivate contractors to remove their equipment prematurely. His observation was that less time would be spent focused on restorative drying goals and returning a building to its pre-loss condition and more time focused on monitoring how much equipment was left onsite and for how long.
For the most part, today’s reviewers do not look at the goal of the drying project; they look at the costs of the job. The measurable cost of the job is more important than the successful drying of a project. But are those clients actually saving money? Did you help them understand the true savings?
Nobody I have spoken with can pinpoint where the three-day drying standard entered the industry. But the fact is three-day drying was incorrect in 2009, and three-day drying is incorrect in 2019. Based on the science we know today, it is not just incorrect, but it is potentially dangerous, and the liability of applying this standard has dramatically increased to both the contractor and the carrier.
Today, the indoor environmental profession knows more about the effects of contaminated indoor environments and the effects of mold on occupants and highly sensitized individuals. If contractors and their customers are not aware of these risks and do not address properly drying a structure, it can dramatically increase the potential for litigation and there is no limit on that liability.
The industry has to do a better job of understanding the terms ‘stabilization services’ and ‘restorative drying’. Today we see many service level agreement protocols that are drafted with the use of terms like “contractors cannot proceed with drying and are to only stabilize the site until an adjuster has provided a confirmation of coverage or until the adjuster has viewed the loss location.” But what does that mean to the contractor?
In the restoration world, stabilization services and restorative drying are two very different stages of the drying process. But they are often misunderstood and misused terms.
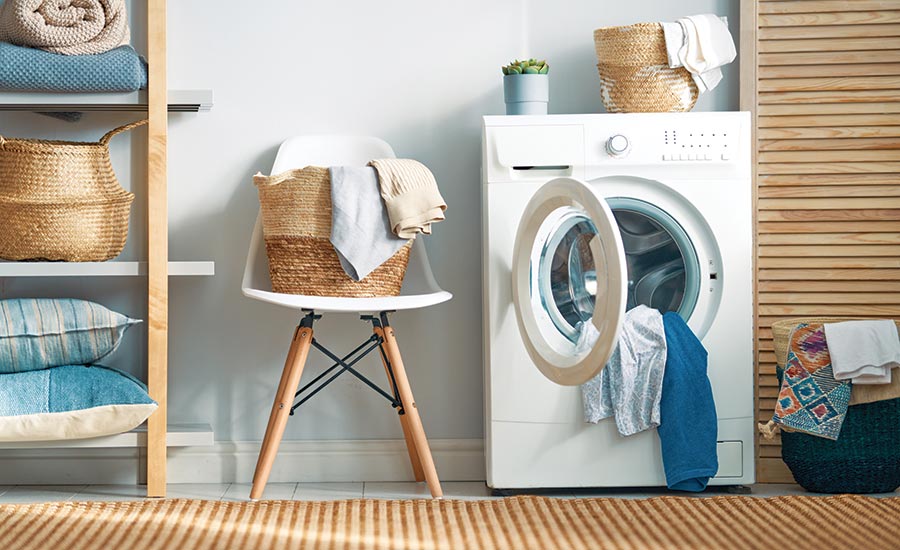
Stabilization Services
Stabilization services are used during the investigation stage of the claim before coverage has been determined or before the hazard assessment is completed. Most commonly, stabilization services are used while determining coverage issues, identifying the cause of loss, determining who is the responsible party, or waiting for testing results of hazardous materials such as lead, asbestos, and now silica. The process gets even more complicated when multiple factors are involved.
Stabilization services serves only one purpose and that is to prevent additional secondary damages that can range from high humidity, prevent cross-contamination to unaffected areas and/or to allow the restorer to secure the job site. In water damage jobs, stabilization services will consist of dehumidifiers and potentially air scrubbers to reduce the humidity and particulate in the air. If the job is left in the stabilization phase a restorer can anticipate the degrading of water in categories and there is a high potential for surface mold growth both on the exterior surfaces and the backside of the materials.
It is also considered stabilization For jobs that require the restorer to spend multiple days removing contents in a CAT 2 or CAT 3 job, they may place the site under stabilization to prevent secondary damages while they work. It is critical that the restorer explains this to their customer as they will often expect that this phase of the job will result in structural drying.
After you have stabilized the job and are ready to proceed with restorative actions your most likely step is going to be to deploy a 3 step/stage bio-wash. We will get into the details of a bio-wash in another article, but for simplicity sake the restorer is required to wash the structure and flush and extract the structure to remove as much of the debris and organic waste that is on the material surfaces and behind sill plates etc. This requires large quantities of water and attention to detail in physically removing the materials. Flush, flood, scrub, flood some more and extract. This will result in saturated materials. Next the restorer can apply their antimicrobial and if the product requires removal of the product you will have to do the flush, flood, scrub, flood some more and extract again. Now you are ready for structural drying... and that’s a good thing because this building needs it.
The Laundry Analogy
Let’s throw in a real-world analogy here. Three-day drying is like saying, “All things I throw in my drier can be dried in 30 minutes.” Sounds reasonable if you have never done laundry. Just crank the heat, just get a better dryer, just take a three-day laundry drying course (LDC to our WRT?) and you are a master of everything laundry. If I were to use my dryer and throw in five cotton t-shirts, set the temperature to medium and hit start, I think I have a great chance of drying those shirts in 30 minutes.
However, would it be reasonable to expect to have the same success if I threw in towels and jeans with the t-shirts? No! I wouldn’t be able to successfully dry all of those items in that time. Wait! What if I just turn up the heat to high and then start drying, surely I can get them done in 30 minutes? Maybe, but you might shrink the t-shirts, you might damage the finishes, and you might need to replace them. But sure, why not take on that liability and try to do the impossible.
It would be insane to say “all laundry can be dried in 30 minutes”, just as insane as it is to say that “all buildings can be dried in 3 days.” You know who makes claims like that? People who don’t do laundry and have never shrunk their favorite shirt. And you know which restorers say they can dry everything in three days are the ones who probably don’t do laundry!
In the next article , we are going to explain the liability associated with the three-day drying method.
Restoration is not as simple as putting equipment into the jobsite and walking away. This mentality is dangerous and does both the customer and the profitability of your business a disservice. In the next article we are going to explain the IICRC’s S500 standard and how the different calculations are interpreted can be dangerous if done incorrectly.