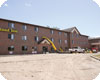
This year’s spring thaws had many river communities in the upper Midwest holding their collective breath, desperately hoping not to see a repeat the historic flooding experienced in 2008. Communities along the Cedar and Iowa rivers in Eastern Iowa were especially hard hit, swallowed by floodwaters reaching nearly 20 feet beyond flood stages in some areas.
The waters did not discriminate. Homes, city infrastructure, universities and businesses alike were infiltrated by polluted river water. In some areas, structures outside of the 500-year floodplain were not spared.
The cruelty of flood damage is that it often occurs slowly, with waters engulfing buildings over a long period of time. Dissecting the communities of Coralville and Iowa City, the Iowa River crested 9 feet above flood stage, and it remained above flood level for weeks. “Water flooded the first floor of our hotel for nearly 10 days,” Joe Minard, owner of the Coralville Heartland Inn, said.
While flooding may occur in slow motion, cleanup efforts must begin immediately and be carried out quickly in order to prevent illness and further water damage to structures.
For the Coralville Heartland Inn, quick action also meant keeping water and humidity damage from migrating to the second and third floors of the hotel, causing secondary damage.
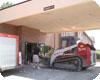
Reserved for Restoration
The Coralville Heartland Inn sits 1 foot above the 100-year floodplain, and its location makes it a hotel of choice for many visiting the nearby University of Iowa. However, its elevation was to its detriment in June 2008 as the swollen Iowa River seeped into 30 percent of the hotel’s rooms.While insurance covered the contents and structural damage, the Coralville Heartland Inn had nothing to cover the loss of business. “This is a significant hotel with high occupancy rates, especially in the summer,” Minard said.
The surrounding 18 Heartland Inn locations were able to make up most of the lost business, but there was a sense of urgency to quickly get the hotel back to pre-flood condition and avoid damage to the floors above.
Since the Coralville Heartland Inn had no service contract for this type of damage, Minard had to start from scratch to select the right restoration contractor and equipment to quickly get the job done right. However, he and many other business owners were overwhelmed with the number of contractors from around the country, offering different drying techniques and philosophies.
“This was the first time a natural disaster of this magnitude hit the area, and the Heartland Inn was the biggest job on the Coralville Strip,” recalls Mike Hambly, president of restoration contracting company Dream Steam Carpet Clean, Inc. “My heart went out to Joe, since it was an emotional time for him and he was being pressured from many contractors selling against each other’s techniques.”
Eastern Iowa flooding kept the Des Moines, Iowa-based Dream Steam busy throughout much of the summer. The IICRC-certified contractor handles more than 200 water damage jobs a year on average, with typical applications ranging from cleanup due to broken pipes to sewer backup.
While the company is well-versed in all phases of restoration work, the sheer scope of the flooding throughout the large, honeycombed structure presented unique challenges.
“There was 3.5 to 4.5 feet of water throughout the entire 25,450-square-foot first floor, which included 55 guest rooms, two elevator shafts, a pool, lobby and meeting room,” Hambly said.
With a long résumé of successful restoration work and personal friendship with Minard, Hambly and Dream Steam were awarded the daunting restoration contract. The contractor immediately started moving in equipment to dry the building.
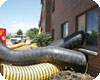
A Two-Pronged Approach
Flooding at the Coralville Heartland Inn represented the most severe form of water damage. “There are three categories of water damage, with Category 1 representing clean water, like a pipe break. Category 3 signifies dirty water,” Hambly said. “If you get to Category 1 damage quickly enough, most items can be salvaged, but with Category 3 damage, few items the water touches can be saved.”Dream Steam took a two-pronged approach to drying the Inn. On floors two and three, they used dehumidifiers and air movers to keep the moisture from damaging any of the upper floor contents. They monitored moisture levels with readings at least twice a day to safeguard against water damage.
As an added measure, the carpeting, furniture and walls received a thorough cleaning. According to Minard, Dream Steam went extra steps to ensure the cleanliness of the hotel, especially since “we are close to the University of Iowa hospital and some of our guests are visiting sick relatives and friends,” he said.
The bulk of the intense restoration effort was focused on the first floor. Everything on that level – furniture, shower structures, toilets, light fixtures, etc. – had to be discarded.
The walls were stripped down to the studs, and insulation and electrical wires were removed. “We went through $18,000 worth of dumpsters,” Minard said.
The remaining studs, windows and exterior walls were then power washed and sprayed with a mildewcide to prevent mold and mildew growth. Every restoration job is unique, Hambly said, and the crews learn a few things every time. “We switched the antimicrobial during the process when we found that one worked better than the other,” he said.
To dry the first floor and prevent additional moisture damage, Dream Steam turned to Star Equipment and Wacker Neuson for specialized drying equipment. Two Dryvex MC5200 open drying systems from Wacker Neuson Climate Control were rented for the efforts.
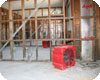
Crews installed the flexible ductwork on the outside of the structure. Inside, more than 150 air movers helped to facilitate the drying process. Crews experimented with air mover and ductwork location for optimal drying. Dream Steam discovered that it was more efficient to section off and dry half of the structure at a time, and remove the water-absorbing contents prior to drying.
Within 10 days, Dream Steam had the structure sanitized and dried. “The MC5200s worked fast,” says Hambly. “There was a much smaller building nearby where the contractors [using a different drying system] were drying the building before we started on the Heartland Inn and were still not done by the time we finished.”
Once the drying was complete and the structure passed a stringent industrial hygienist test, Minard’s other company, Joe Minard Construction, completed the reconstruction phase on the first floor.
On Sept. 30, 2008, the renovations were finished, and the Heartland Inn was once again welcoming guests at their Coralville location. “We were very pleased by the hard work of Dream Steam and the service received from Wacker representatives to quickly get us back in business,” Minard said.
Report Abusive Comment