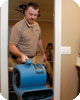
One of the questions I get repeatedly during classes and at breaks is, “Is there a flowchart or check list for doing a job correctly from start (the phone call) to finish (getting paid on time)?” Then Clark, an adjuster with whom I recently had the pleasure of teaching the new IICRC CDS class, asked me the same question, to which I responded, “No water loss is the same; the jobs are just too diverse.”
True, each job is unique…but might there be some fundamentals to focus on that are common to most every job? I am going to give it a shot, with a disclaimer: what follows here is some of the basic fundamentals; many will say they need to be added to, which is exactly the point: take what you can from here, add to them and make the project yours.
If you feel so inclined, please e-mail me and we can discuss the points. Who knows; we might come up with some topics that lead to future articles.
The goal here is to make us all better dryers. Of course, experience and classes will refine your final jobsite decisions. The process of restorative drying is truly still more art than science, though we are working hard to change the balance.
I am just one guy with one opinion and, as no two jobs are the same, here is what I have come to lean on over the years.
Administration & Training
- Paperwork – First Call Check List; Contract; Equipment Installation List; Daily Humidity Log, Materials Moisture Content Log; Change Orders; and your Satisfactory Completion and Payment Authorization Form. Have it all organized.
- Contract – Visit a general contractor-focused attorney who is also a litigator. A contract needs to minimally include: scope of work; payment terms and penalties; satisfactory completion criteria; pre-existing conditions; right to remove and dispose of personal property; lien privileges; contractors’ rights privileges and liability limitations; hold harmless agreement; personal guarantee of payment and what insurance coverage, if any, is available.
- Paperwork must be filled out and kept for future review if necessary. Establish a process and stick with it. In court, if you cannot prove you did it, then you did not!
- Training – The minimal training certifications I’d encourage are the IICRC’s WRT (Water Restoration Technician), CCT (Carpet Cleaning Technician) and HST (Health and Safety Technician). I would highly recommend ASD (Applied Structural Drying Technician) or ADI, as well as AMRT and CDS certifications for crew chiefs. (For more, go to www.iicrc.org.)
- Licenses and insurance; vehicles; supplies; PPE; extractors; air movers; dehus and quality thermohygrometers and moisture meters for drying and recording data.
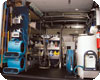
On-Site Inspection
- Determine the Category of water and record it, per the IICRC S500 Standard. Photo-document all areas and contents, wet or dry, and any source of water.
- Determine the extent of migration. Be sure to check well beyond obvious wet areas; water can skip floors or rooms when spreading. The area needs to be mapped and documented for drying progress, and checked and recorded daily (dry materials have been known to get wet on day two).
- Evaluate contents with customer and, if possible, the adjuster, and determine what is to be restored and what is to be removed and disposed of. Get the Personal Property Removal/Disposal form signed.
- Establish expectations and satisfactory completion criteria and get the contract signed; after that, go ahead and perform a thorough extraction and position contents.
- Is the building to be occupied or vacated during the restoration? You always dry faster in a vacated facility, but business interruption insurance or customer desire may require them to stay in operation during the job.
Select and Install the Proper Drying System
- Take ambient, affected and unaffected air RH, temperature and dew point readings and record them on the Daily Humidity Log.
- Determine what temperature and humidity you want the entire structure or parts of the structure kept at. This becomes your Environmental Conditions and Materials Temperature goal.
- Is mechanical dehumidification necessary, or will Mother Nature and temperature control alone be enough to achieve these goals? Select equipment accordingly. Remember, you need to be able to prove where the water went.
- Are you going to remove base and perforate walls, or dry in place? Destructive operations are faster, but drying with walls intact is less obtrusive. See Dri-Eaz’s “New Guide to Restorative Drying,” chapter 9 for a flowchart on page 133.
- Determine the facility’s available power. Install drying equipment, turn on the microwave, TVs, entertainment centers, gaming units, hair dryers, etc. and see if you blow circuits; if so, you will have to reroute power.
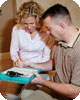
Monitoring the Project
- People turn off equipment due to temperature, noise and blown circuit breakers. If the building is to be occupied during drying, install the quietest fans and dehus you can, and ensure that there are no blown circuits due to occupant power use.
- Chase the water. Monitor the job at least daily, move (and document) equipment to maximize evaporation and record all environmental and material readings.
- All the moisture content numbers should be going down, indicating evaporation is taking place. Record them using wood moisture equivalent or relative numbers, and indicate the Drying Goal or Dry Standard number you are looking to achieve.
- Readings and record keeping is now a lot less painless with data loggers, real-time monitoring and mapping software with built-in reports. Explore what technology is available to help you.
- Not evaporating? You may need more access to the water source. Will spot heat be adequate to increase evaporation, or does the source need to be removed? Is a Change Order necessary?
Wrap It Up
- Record the removal of all the equipment, including serial numbers and the condition of each piece. This should match your Equipment Installation List. Record the return of all the personal property removed, include photos and condition. This should match your Personal Property Removal List.
- Walk through with the materially interested parties and take readings and pictures of event. Get your Satisfactory Completion and Direction to Pay form signed.
- Produce billing within 24 hours of project completion and expedite to the correct billing address. Include a project description, photos and saved property value in dollars for replacement comparison and drying justification.
- Call within 2 to 5 days and inquire if the billing is correct or if attention is required.
- Call 25 days out to accounts payable office to obtain the check number and when it will be issued. If there is a problem, correct it. If they are not paying, you may need to file the Workman’s Lien that you received privileges for in the contract. You have a limited time to act.