In the early part of the 1900s, a woman named Mary Mallon worked in the New York City area for several families. She appeared healthy, yet she was a carrier of a deadly disease and the cause of several serious outbreaks. She’s presumed to have infected 51 people, at least three of whom died. One of the reasons she spread the disease so easily is that she was a cook and didn’t believe in personal hygiene. Today, she’s better known as Typhoid Mary.
While the cleaning equipment you use is inorganic and unlikely to cause such a scenario, the question remains: Should you regularly clean and decontaminate it, especially after cleaning such areas as healthcare facilities or the residence of a hoarder where pathogens exist? What about areas where there was a serious mold contamination problem?
Although medical buildings may not look dirty, most of their carpets, flooring, and furniture have contaminants that are easily dispersed by air movement caused by vacuum cleaners, dust mops, or even just being brushed against. Once scattered, those contaminants can end up in and on your equipment and could potentially infect others. (For instance, most studies have shown that the flu virus can live and possibly infect a person for up to 48 hours after being deposited on a surface.)
But what you need to be concerned about the most are mold spores. The Institute of Medicine (IOM) found there was enough evidence to link indoor exposure to mold with upper respiratory tract symptoms, cough, and wheezing in otherwise healthy people. Mold spores travel through the air and attach to virtually everything, so they easily transfer from place to place, affecting those who suffer from allergies or asthma.
For example, it’s very common for families who escape from a mold-polluted residence to cross-contaminate their new place of residence to which they move by carrying the spores on themselves, clothing, and possessions. You can do the same by not decontaminating your equipment.
But, cleaning equipment before leaving a contaminated jobsite is essential. Otherwise, the vehicle you transport it in will itself end up with mold spores. Then, even if the equipment is cleaned back at your shop or warehouse, it can again become contaminated once it’s loaded back into the same truck—and you’ll carry those mold spores on to the next job.
If your equipment has been used where the flu virus is rampant, wash the surfaces with a general household cleaner to remove grime, then rinse with water and apply an EPA-registered disinfectant to kill germs. Be sure to read the label to confirm it’s EPA approved for effectiveness against influenza A virus. If a surface isn’t visibly dirty, clean it with an EPA-registered product that will both clean (remove germs) and disinfect (kills germs) instead.
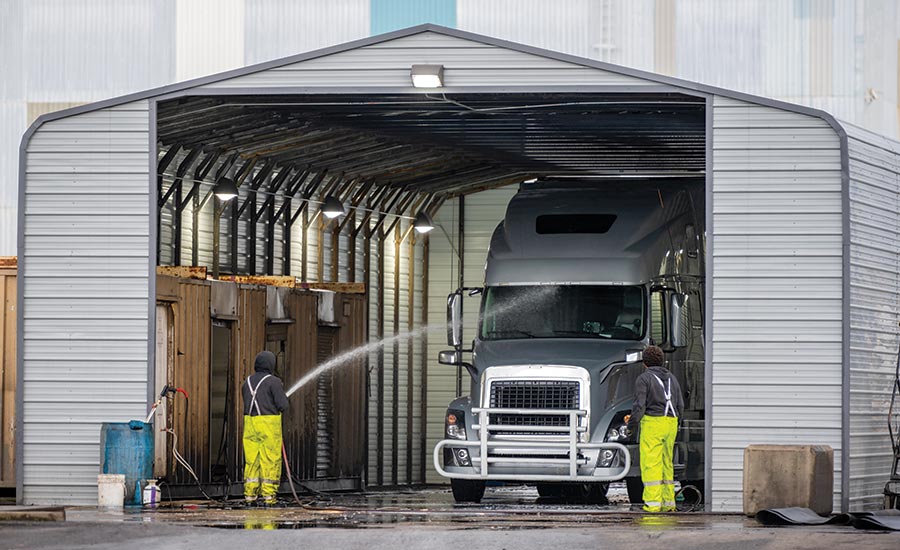
If there was mold contamination at your last job site, wipe down all surfaces of your equipment with a disinfectant like Benefect or Sporicidin. Be sure to also replace the filters in vacuum cleaners and any portable air filtration devices before using them again. Recovery tanks on portable carpet cleaning extractors should also be flushed out and cleaned to remove any pollutants that were picked up on the worksite.
Granted, contamination may not happen on every job. And while air movement may scatter contaminates, that same air movement also makes it very hard for microbes to grow, including mold. Since every job is different, you’ll have to make a judgment call. But it’s a good habit to go ahead and clean your equipment after all jobs anyway. Doing so not only makes the units more presentable to your next customer—after all, who wants to see dirty equipment being hauled into their home or business?—but also ensures you won’t end up becoming a “carrier.”