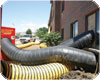
The idea of “green” or sustainable equipment and practices is nothing new, yet finding a consensus on how to incorporate green techniques and ideas in a restoration program is harder than you might think. To try and set a baseline from which to start the conversation, R&R asked Trent Massey, Corporate Social Responsibility Practitioner and Property Programs Instructor for Arlington, Texas-based Vale Training Solutions, if he could help shine a light on some of what’s going on today – and what’s to come – when it comes to restorers “going green.”
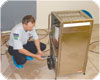
Restoration & Remediation: Let’s start at the beginning. There’s a difference between restoring and replacing; when it comes to a LEED-certified building, what does that mean for the restoration professional?
Trent Massey: LEED buildings can be challenging to the restoration professional for different reasons. One important issue is that a variety of installed ‘green’ materials may have contributed towards the points that helped earn the LEED label. Those labels are earned for the original LEED specs. When these green materials are damaged and deemed necessary to replace, the original integrity of the LEED rating must be retained.
The challenge is finding suitable replacement materials, other than the exact make and brand originally installed. If replacing damaged original materials which may be green with traditional not-so-green like, kind, and quality construction materials, then the LEED label may be suspect. Traits which help identify green materials can include recycle content percentages (percentages matter too); regionally extracted and manufactured materials; low emission materials; products made from rapidly renewable sources; lumber from certified forests; products which helped reduce waste; products which contribute toward a reduction in energy or water use and much more.
Restoring the building’s materials over replacing is at
present the best option to helping retain the original LEED specs. When we keep
the original materials, the documentation on the LEED building stays
valid.
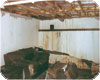
R&R: When it comes to equipment, while every restoration is unique, is it fair to say that the less equipment put into use, the better?
TM: Restoring a green building requires it to be done right, just like traditional buildings. If drying a green building, the restoration professional must ensure the job has the appropriate amount of equipment in place, performing as designed. To cut back on equipment just to save energy (perhaps thinking this will appeal to the owners of a green building) may not always be smart. Leaving the building with problems later like musty smells or even mold will make no one happy.
A green building should have a tighter envelope, higher efficiency HVAC systems, overall better (before loss) indoor air quality, and building materials which may not endure water too well. These all may come into play when calculating equipment needs. I could see the case where sometimes more equipment might be required.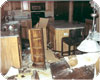
R&R: Talk a little about demolition, disposal and removal, and how the idea of “an empty Dumpster is a green Dumpster” applies.
TM: “An empty Dumpster is a green Dumpster” is a phrase we have been saying to our students for awhile. The idea of an empty Dumpster or no Dumpster connects to many talking points which help describe a greener restoration process. First, better indoor air quality is a trait of many green buildings. Concerning repairs, there are a couple common paths which contaminants like construction dust enter a building. The first way is through the demolition process and the second path is when materials are replaced.
Demolition of drywall, tile, and other materials typically produce dust which has to be contained and of course these materials need a Dumpster to be carried away. Cutting and installing new drywall, MDF, fiber cement siding, and other materials also leads to dust in a building. This new dust too has to be contained as well as the new material scraps hauled away – another need for a Dumpster. Simply stated, demolition and replacing implies dust and a Dumpster.
It takes fuel to transport Dumpsters to and from job sites, and I’m not sure when or if a contractor thought twice about the distance or fuel consumed moving a Dumpster from a job site to the landfill. We don’t have landfills in every community, you know.
Finally, the empty Dumpster may also mean the job is
completed sooner which helps minimize claim issues like Additional Living
Expenses on residential losses and Business Interruption expenses on commercial
insurance claims.
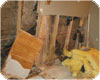
R&R: What are some of the most common misconceptions restorers and insurance professionals have about “green” restoration?
TM: Some of the misconceptions or myths we hear at times include “It cost too much,” “We don’t have time,” “No one cares about it,” and I have also heard the opposite, “Isn’t everyone doing this.”
Let us address these myths. First, I’m sure most everyone is not offering green restoration; at least we see little evidence of it. I’m hoping that someday the majority restoration industry will have ‘sustainability’ as the main component in their business models but that day is not here.
In regards to no one caring about green, I have witnessed the contrary. One of our students was awarded a $300,000 fire loss after graduation simply by offering green and backing it up with their credentials. I have also attended open house events on new green homes along with 3,000 other individuals interested in seeing the benefits of green homes. I do not think those green open house attendees would object to a green restoration project should one be offered to them later.
With regards to green restoration projects taking too long or costing too much, that all depends. The issue of time depends on the owner’s ability to make decisions quickly, the availability of materials, the knowledge of the restoration professional managing the project, and other factors. Yes, a green restoration project can take longer, or it might not.
Regarding costs, if we are talking about replacing damaged traditional materials with green alternative materials, then the answer depends on the selections by the owner of the building. If we are discussing an insurance claim with a set budget, then there are materials on the market today with only marginal cost over traditional materials.
It also depends on the original budget of the damaged item. Flooring, paints, engineered lumber, roofing, appliances, and more are just a few examples of product categories where alternative green materials can be found within reasonable pricing and sometimes for the same. There are also products which can cost a lot more. This is where the education and preparation of the restoration professional pays off too.
R&R: Equipment is expensive, but so is energy. Older and poorly maintained equipment uses more energy than newer, more efficient machines. Any recommendations for companies weighing whether or not to purchase new equipment vs. staying with what they’ve got?
TM: If they work, keep them for now, use them when you must. I understand the incentives for getting rid of the old and bringing in the new. Less energy consumption means more equipment (like air movers) can be running on an electrical circuit. You can still trip breakers though and homeowners will still shut these newer ones off at bedtime. (Truly, quiet is green too at bedtime). Meters and remote monitoring systems are good for these reasons and more. When having to rely on generators for power, then there is that incentive too for using more efficient equipment. I get that less energy is better and helps with a greener restoration project.
In the restoration world, there may be times (as in catastrophe) where we need this older restoration equipment, and so they serve a greater purpose. In poor economic times too, it is just not financially feasible to swap older equipment for new. Being in the red over an untimely green purchase is not good either. But certainly when an older unit has failed and no longer dependable and worth keeping in service, then that is probably the ideal time to replace with new or newer while weighing the overall cost and ROI to the business. The restoration industry is still a business so finding a balance of how to best address older equipment in a win-win decision is best.
R&R: Crystal ball time: Where do you green and sustainable restoration practices heading in the next 10 years? Will we see a set of best practices, or even a universally accepted Standard come into existence?
TM: First, we easily see a day coming in the next 5 years where restoration professionals serving on insurers’ vendor networks will be required to have in place a working Corporate Social Responsibility (CSR) plan which will include a component for sustainability in its business model. Green restoration will be part of this sustainability provision too. We see a scenario unfolding where if the restoration professional does not have a CSR plan, they will no longer receive claims on the network. In Canada we have already witnessed at least one insurer requesting its vendor contractors to adopt a sustainability plan. We do not see the insurance industry as being exempt from this trend. Our best advice is for the restoration industry to get on board now rather than wait. There is also a bottom line element here with a CSR plan. Companies with successful plans are seeing their expenses reduced and profits increased.
Regarding best practices, we certainly believe a standard for green restoration practices will be debated and eventually created. We don’t have this yet. I have already bought the binder and labeled it the National Green Restoration Standard and we bring it out in our current classes, but as of this date it has not been written by the restoration industry. My students laugh when I show them the empty binder. Until such time we have formal best practices or a national standard, we have written a White Paper titled “The Responsible Restoration Company” which helps describe what we see as the first real guideline for the green restoration professional of the future.
For more information: