When Hurricane Irene unleashed its fury in eastern Maryland one August night, the storm spared no one in its path – including Dorchester General Hospital in Cambridge, Md. Violent winds and heavy rain caused extensive damage to the hospital.
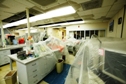
When Hurricane Irene unleashed its fury in eastern Maryland one August night, the storm spared no one in its path – including Dorchester General Hospital in Cambridge, Md. Violent winds and heavy rain caused extensive damage to the hospital, requiring the evacuation of all patients and the closing of the facility for repairs. However, it was critical that the facility reopen quickly. With the help of a disaster restoration specialist, the hospital opened less than a week after the storm.
Dorchester General Hospital (DGH) of Shore Health System is a 52-bed community hospital, providing 24-hour emergency services. The hospital, a three-story brick building built in the 1960s, primarily services Dorchester County, although it also treats patients from nearby Caroline and Talbot counties.
On Saturday, August 27, as Irene roared up the eastern seaboard, staff on site in the DGH command center hoped for the best, but were prepared for the worst. Soon, heavy rain and violent winds began pummeling the hospital facility. By late Saturday night, after hours of wind-driven rain, the flat gypsum roof of the DGH laboratory, a one-story facility on the east side of the hospital, began to leak. For the first few hours, hospital personnel managed the leaks by catching water with cans, and using mops and wet vacs. They also placed protective plastic sheeting over the sensitive diagnostic equipment in the lab.
Their efforts, however, proved fruitless when strong winds ripped the lab roof open, allowing gallons of rain water to pour into the building.
“By 1 a.m. on Sunday morning the wind had really picked up, the rain was coming down in full force and the leak in the lab had become sheets of cascading water,” said George Shoener, facilities management director for Shore Health System. “We quickly realized we had to abandon collecting water and just wait until the storm subsided.”
By 2:30 a.m., damage from the storm was overwhelming. Although the lab sustained the most severe water damage, other areas of the hospital experienced leaks because of the punishing rain and wind that penetrated the building’s windows and brick façade.
Also taking on water were the patient rooms and the chemotherapy suite on the second floor, and the pharmacy, operating room and central supply rooms on the third floor. All of the floors on the north side of the building were moist and many walls throughout the facility were soaked.
Without the ability to conduct lab testing, perform surgeries and dispense medications, hospital officials had no choice but to close the emergency room and move patients out of the facility.
The evacuation of DGH began at 7 a.m. on Sunday, August 28. Approximately 30 patients were transferred by ambulance to Memorial Hospital, located 20 miles away in Easton, Md., while patients in the behavioral health unit were relocated to Eastern Shore Hospital Center across town in Cambridge.
With evacuation efforts underway, DGH facilities manager Robert Hurley turned to Polygon, a disaster restoration specialist. Jeff Cox, temporary humidity control project manager with Polygon, arrived on site within 45 minutes of Hurley’s call.
“Polygon was on site Sunday morning,” said Shoener. “Jeff performed an assessment and began ordering equipment and personnel so we could immediately start drying the building to prevent mold growth and the need for reconstruction.”
Sandi Taylor, project manager with Polygon, also arrived to manage restoration efforts. Shoener advised Taylor and Cox of the hospital’s ambitious goal to have operating rooms and the emergency wing operational by Friday morning – less than a week’s time.
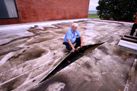
Throughout the project, Polygon technicians used infrared cameras to check the moisture levels and drying progress of various building materials.
In addition to drying efforts, Polygon coordinated the work of the specialty contractors retained to handle renovations. Shoener hired Tecta America East LLC, a national commercial roofing company, to repair the lab roof. Willow Construction, a general contractor based in Easton, Md., replaced or repaired the plaster walls, ceilings and drywall that were damaged and provided general construction support.
Polygon facilitated the removal of debris as well and handled the final cleaning of affected areas. On Monday, August 29, Polygon had 25 skilled laborers on site, outfitted in appropriate protective suits, with specialty equipment and solutions, and working either day or night shifts to remove debris and clean areas.
“An area was contained, ‘rough cleaned’ for debris removal and then every square inch cleaned and disinfected utilizing hospital grade chemicals and procedures,” said Taylor. “Cleanliness and quality control were extremely important to insure IAQ standards were maintained and to meet the stringent requirements for a hospital setting.”
Polygon technicians and skilled laborers were on site 24 hours a day throughout the duration of the project. An insurance adjuster made a site visit and was satisfied with the plan and goals set by the management of the hospital and Polygon. Taylor was on site for the duration of the project, sometimes for 18 hours at a time, working with the director of the lab, ER and pharmacy suites to coordinate efforts and provide progress reports.
“Sandi kept me and the rest of the hospital staff fully informed of how the drying operation was proceeding,” said Shoener. “She had the proper equipment to measure areas that were still damp, the right equipment to isolate areas of the hospital that they could dry, and simultaneously had teams available to clean those areas ready for cleaning.
“Due to Polygon’s sophisticated drying expertise, we were able to save about 80 to 90 percent of the walls and other building materials that were wet and damaged,” added Shoener.
The specialty cleaning process was completed at 7 a.m. on Thursday, September 1 in the targeted areas and verified through testing by an independent third party industrial hygienist, Susan White with Sussex Environmental. Areas tested included the lab, operating rooms, and sterile supply areas. All of the air samples and swabs for mold, bacteria and virus were negative.
“The independent testing enabled the hospital staff to return to their work areas and the hospital to receive patients again on Friday as was the hospital’s goal,” said Taylor.
Officials from the Maryland Department of Health and Human Hygiene conducted a walk-through of the hospital and gave final approval to reopen.
Patient care resumed on Friday, September 2.
“To reopen less than a week after the storm was an amazing feat,” said Shoener. “Our staff and our partners at Polygon, Tecta America, Willow Construction and other vendors were tireless in their cleanup, drying and repair efforts.”