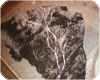
For most mold remediation professionals, imagining a section of fungal growth as anything resembling a work of art is a stretch of the imagination. To a professional contractor in British Columbia, however, stepping back after a successful remediation job inspired that unique perspective.
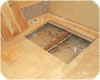
Interior design ideas aside, Hessel knew he had a substantial job at hand. In mid-October 2010, a couple in Cranbrook, B.C. called for help with what they felt sure was a serious mold problem in their basement. The job, which took approximately six weeks, required demolition and tear-out of the entire basement area.
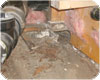
The team quickly confirmed the homeowners’ fears. “I could tell from just the initial examination of the basement that we were up against one of the most extensive and pervasive amounts of mold growth I’ve encountered,” Hessel said. “The entire basement set-up, which included space for a living room, bathroom and laundry area was, to some degree, water and/or mold damaged.”
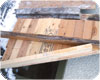
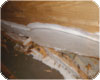
The hygienist’s report indicated several long-term causes were likely at play. A hot water tank leak 10 to 15 years before was apparently inadequately mitigated and dried. Damp and dirty building materials were stored for years in a space under the stairs. Finally, poor exterior drainage led rain and snow melt to run predominantly toward the home at the basement level.
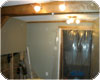
While exterior visible water damage was limited primarily to the concrete foundation, a bonanza of mold growth occurred within basement walls and floor system. The concrete and walls covered in tarpaper featured 2x4 wood framing, vapor barriers and either drywall or wood paneling. The concrete floor was covered by a sleeper section environment consisting of 2x4s standing on edge topped by ¾-inch spruce plywood. In between was a 3½-inch gap that, given years of unchecked exposure to invasive moisture, provided a lush yet relatively hidden microcosm for fungal growth.
“What we observed,” Hessel said, “was essentially a house being devoured from the inside-out by a slow, unrelenting and destructive invader. The ‘soft spot’ found by the homeowners was the warning siren for a serious problem.”
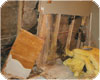
A deeper investigation into the flooring cavity using a borescope revealed further damage. To be as non-invasive as possible in their initial look, the team drilled four small holes in different locations and snaked in the borescope. Images relayed back showed oddly-shaped and eerily-arrayed mold growth patterns almost alien in appearance.
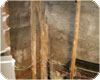
Most of the worst mold growth was detected in these sleeper areas. Due to the multi-purpose use of the basement, a variety of flooring was installed, including tile, carpet, laminate and vinyl. An additional type of flooring, however, provided an extra twist and challenge to the overall remediation job.
“Previous owners had installed asbestos vinyl tiles,” Hessel said. “Extra precautions were required to ensure the safety of my team, the homeowners and the environment.”
Hessel and his team used polyethylene sheeting to fully isolate the basement work area and installed a negative air unit with high-efficiency HEPA filters to scrub and help maintain negative air pressure. The asbestos vinyl tiles were removed and placed in six-millimeter plastic bags clearly labeled “hazardous materials.” British Columbia provincial law allows for this type of bag to be used for asbestos vinyl tile.
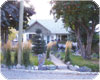
Another challenging aspect of the job came in removing demolished materials from the basement. The basement offered no windows that would open, only 1½ x 2 ½-foot double-pane Plexiglas slits set high on the walls.
“Given the environmental isolation of the basement work area, using the stairway wasn’t an option,” Hessel said. “So, with the homeowner’s permission, we detached one of the Plexiglas slits. We then had the challenge of reducing every piece of demolished material down to a size small enough to squeeze through that window. It was a tight fit and required creative thinking and extra muscle. In the end it worked and maintained the environmental isolation of the basement more efficiently than repeated hauls up and down the stairway.”
Hessel had a maximum crew of five restorers on the job, one of whom was always posted outside by this window to take the demolished materials.
After Hessel and his team completed their work, the hygienist’s fungal remediation job summary told a different story. Total spore count in the isolated work area decreased 3,142 (fs/m3) to 742 (fs/m3). Counts from the basement floor cut-out continued this successful trend with the leading culprit, penicillium/aspergillus dropping profoundly. The report further indicated, through pre and post-job site inspections and sampling, that Hessel and his team successfully completed remediation of fungal-contaminated materials according to the scope of the job.
With the potential for adverse health conditions from indoor mold exposure as reported by the Environmental Protection Agency and Health Canada, this came as good news to all parties involved.
“The asbestos vinyl tiles, tiny basement windows and sheer extent of fungal growth did pose extra challenges to our team,” Hessel said. “Working together, we were able to take care of our customers, show respect to people and property, and remediate a really nasty mold situation. All in all, not a bad day’s work.”