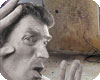
A few years ago I was asked by the International Conference of Building Officials (ICBO) to review their International Existing Building Code. They were interested in my take on the section related to ventilation and mechanical systems, and wondered if I would provide comment from a property restoration and remediation contractor’s perspective.
They were particularly interested in how building codes can impact indoor air quality and how code revisions might help to prevent water damage and the subsequent formation of mold.
I was delighted to have the opportunity for input so I read the code thoroughly. The ventilation and mechanical systems section appeared to be comprehensive. It dealt with fire safety and prevention, reconstruction, and standards for access, ingress and egress.
What struck me as odd was there was very little information on construction practices designed to avoid or reduce water intrusion. The code also lacked guidance for source control of indoor air contaminants such as mold and bacteria resulting from water damage to the structure or the mechanical system.
I was excited! Finally, someone in the regulatory community had noticed our little service niche known as restoration and remediation and we could begin to make a difference.
I proceeded to tell them about our extensive knowledge base and our scope of capabilities. I told them how we deal with the restoration of properties damaged by fire, flood and smoke. I discussed our role in promoting indoor air quality as well as our competence in the remediation of mold, biohazards and other contaminants necessary to return properties to a pre-loss condition.
Restorers and remediators are rarely involved in new construction. But we do rebuild damaged properties and want to share what we know about mold prevention with our clients.
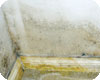
We see loss every day, and we cannot help but have compassion for those who suffer because of it. But what can we do? We aren’t builders…or are we? Many of us do rebuild the damaged areas. Whether subcontracted or in-house, we install new flooring, drywall, base, finish work and paint. But how does our work impact future losses to the property?
When you rebuild, make recommendations to reduce the amount of damage caused by water intrusion. This is an excellent time to impart your knowledge. They have just vowed to never let this happen to them again and will be very interested in making changes such as upgrading to moisture and mold resistant materialsMost of you have seen dozens if not hundreds of floods and you have likely learned the cause of each one. This mental database can be valuable to your clients.
You can also share with them some of the lessons and tips you’ll learn here, such as installing burst-proof supply lines on their plumbing fixtures. While you may not actually do the work (especially plumbing or electrical) you will still help the customer avoid another painful experience. They will see this as providing a value-added service.
There is little need to explain the dangers of mold. Your customers already know that left unchecked, mold rots wood and damages drywall. They also know that mold can contribute to poor health. In 2005 a survey conducted by CertainTeed, a building materials manufacture, reported that approximately 55 percent of homeowners expressed concern about mold.
And just last year, the USEPA stated the following in its May 2007 report: Environmental and Sustainable Technology Evaluations Verification of Microbial Resistant Building Materials:
- “About 90% of the interior finished surfaces of buildings are covered with gypsum products
- Last year the US produced nearly 50 million tons of gypsum board and approximately 5 million tons wound up in landfills, most due to moisture and mold damage
- Mold can be found in any non-sterile environment and upwards of 40% of all homes in North America contain fungal growth with gypsum wallboard being a primary growth material
- Gypsum building materials often become wet, resulting in mold growth that negatively impacts health and productivity as well as increases liability and the risk of lawsuits
- The rapid growth and dispersion of mold can induce allergy and asthma episodes, while sometimes producing severe illnesses including pulmonary, immunologic, neurological and oncogenic disorders”
It’s no wonder gypsum wallboard manufacturers have geared up to produce a more moisture and mold-resistant wall covering product.
Other companies are developing products that can be applied to building materials such as structural framing after it has been placed into service. These new coatings retard growth or even kill microorganisms. One chemical that appears to be effective is a micronized copper wood preservative. Introduced to the market in 2006 to help prevent soft rot, the copper particles are very small and can penetrate the cell walls of the wood better than previous versions.
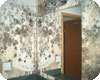
Mold-resistant materials and coatings are not a substitute for good building practices. Just as complete source removal is critical to effective deodorization, we need to eliminate the opportunity for water intrusion before it enters the structure. Proper roof pitch and window flashing; minimal roof penetrations; a well-drained, weather-resistant envelope; and other design elements can reduce the likelihood of moisture penetration. Mold-resistant drywall provides a layer of extra protection, especially in high-humidity areas such as bathrooms, kitchens and spa areas.
The Builder’s Guide (Harriman and Leslie 2006) is written for developers, designers, builders, and owners wanting to know how to reduce the risk of mold growth. It is based on an understanding of the causes of mold problems in new construction. Written by a wide variety of industry experts, it discusses how such problems can be avoided.
The Guide offers a three-part strategy to reduce the risk of mold:
- Keep most of the water away from the house through a few critical landscaping and drainage decisions made by the developer, designer, builder, and owner.
- Keep the rest of the water out by ensuring the roof, walls, and foundations shed and exclude water consistently while draining it away from the house.
- Limit mold growth while moisture dries out by stopping water leaks and spills from spreading indoors and by choosing materials and assemblies that are less prone to moisture retention or mold growth when challenged by occasional wetting.
By the time we are called in, it’s usually too late for flood prevention planning. The best we can hope for is to be able to build back properly with moisture and mold resistant materials and make recommendations for the future. And I do want to stress that the future will be in promoting safer environments through the prevention or minimization of biohazards.
There may also be a niche market helping contractors understand how to build to prevent moisture. Mold contamination caused by construction defects, or simply using wet or moldy materials left unprotected on the jobsite, can translate into costly callbacks for remediation, especially if mold is found in the drywall. Even framing materials delivered from the lumberyard can have active mold growth on them. Any new construction not yet “dried-in” will suffer from water damage during wet weather. Properly drying out these structures before installing the wall and floor coverings can prevent expensive repairs in the future.
Helping people is what we do, and we can make a huge difference in people’s lives. But one word of caution is in order. Before you go advising clients on how to change their buildings, be sure you know what you are talking about. Offer suggestions, but always disclaim instructions outside of your realm of expertise. Structural issues, for example, may be better left to an engineer to resolve.
Here’s a breakdown of five different areas of concern, and some tips and thoughts on how to help reduce the opportunity for mold to develop.
Mechanical
- Emphasize the importance of fresh air ventilation to dilute indoor air contaminants and to prevent or reduce the formation of mold in condensation.
- Provide outdoor relief air for all combustion appliances.
- Don’t install heat registers under kitchen sink base cabinets (chemicals and cleaning compounds are typically stored in the hot environment of the cabinet causing accelerated off gassing and potentially harmful chemical combinations).
- Improve attic ventilation.
- Never terminate an exhaust vent in the attic or crawl space (dryer vents, kitchen and bath exhaust fans, etc…).
- Ensure “A-coils” properly drain into drip pans, and that pans and drain lines are kept clear.
- Seal all crawl space vents and consider installing negative pressure fans.
- Avoid appliance back drafting from negative air pressure caused by clothes dryers, bathroom and range exhaust venting, combustion appliances and whole-house fans.
- Use non-porous ducting instead of fiberglass “ductboard” when replacing or repairing HVAC systems.
- Provide fresh air inlet to return side of HVAC system to meet ASHRAE 62.
Electrical
- Install flood/moisture sensors in water prone areas (below grade, laundry, etc…) to reduce the extent and severity of damage from a water intrusion event.
- Use fail-safe sump pumps (battery back up and alarm system) in high water table conditions.
- Link bathroom vent switches to bathroom lighting circuit (residential).
- Consider the use of ceiling fans or forced air ventilation systems to circulate air within the structure and to avoid condensation and stagnant air pockets.
Plumbing
- Avoid freezing and bursting of supply plumbing through material selection, placement and installation of pipe insulation where applicable.
- When possible, turn off water when leaving a building vacant for more than a couple of days.
- Don’t leave home while automatic dish and clothes washers are running.
- Retrofit supply and DWV systems for simplified draining in northern climates.
- Regulate water pressure for plumbing systems and install automatic main shut-offs upon rapid pressure drop (burst pipe protection).
- Specify drained catch pans under water heater installations.
- Route water heater pop-off valve extensions to drains or outdoors.
- When reinstalling water-fed appliances such as refrigerator icemakers and dishwashers, make provisions to minimize damage from future plumbing failures. Avoid routing copper feed lines through wall or floor cavities, use catch basins and water sensors to alert you to a leaky line. Do not use plastic supply lines.
- Install single lever, double valves or automatic cut-offs for laundry hook ups.
- Install burst proof (stainless steel braided) supply lines to toilets and appliances.
- Provide good access to plumbing where there is a potential for leaks to develop.
- Urge the client to get plumbing leaks repaired quickly and to watch for loose toilets indicating a failed wax ring.
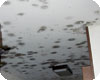
- Keep materials dry and clean on the job site. If not, you will be giving mold a place to thrive.
- Use water-resistant or waterproof materials wherever practical. Use mold-resistant gypsum board or “green board” in wet areas such as bathrooms.
- Consider using mold-retarding coatings on below-grade structural materials
- Avoid excessive use of stud wall blocking and designing inaccessible wall and ceiling voids that can trap moisture.
- Prevent formation of condensation (window glazing and sills, cold water pipes) through the use of thermal breaks and pipe insulation.
- Sink base cabinets are especially prone to trapped water pockets below cabinet decks.
- Provide for ventilation designs and improved water retaining cabinet floors.
- Properly install vinyl cove base tight to floor to prevent mop water and spills from penetrating to the sill plate and wall covering.
- In bathrooms caulk wooden trim to the floor with a bead of caulk under the boards as they are installed. Avoid using MDF or composite trim in wet areas and back and end-prime all trim and base boards.
- Caulk cabinet bottoms where they meet flooring to keep water out.
- Consider sealing the underside and backings of cabinets before reinstalling.
- Avoid the use of particleboard or similar non-water resistant composites as underlay in potentially wet areas (baths, kitchens or below grade floors).
- Install all wall covering materials at least ½ inch off of the floor to break capillary action if floors become flooded.
- Use care when installing insulation as thermal gaps can allow condensation to form.
- Suggest regular inspections for, and identification of excessive structural moisture.
- Avoid re-installing fiberglass insulation in floors above damp crawl spaces. Use rigid foam panels that are mold and moisture resistant.
- Recommend replacing flooded carpeting with vinyl or ceramic tile flooring in basements.
- Install a vapor-retardant barrier over damp earth in crawlspaces. Apply all vapor barriers exactly as specified to avoid trapping moisture in unwanted areas.
Exterior
- Keep water out of walls and other cavities by properly installing materials where water intrusion might occur. These include windows and doors, thresholds, steps, patios, siding, trim, weep screeds, exterior light fixtures, roofing materials, roof and chimney flashing, sky lights and other penetrations.
- Provide for adequate attic ventilation to prevent ice dams at eaves.
- Before installing a new roof, use Ice Shield or equivalent water-proof membrane in freezing climates to reduce roof leaks caused by ice dams.
- Use caution when installing or repairing synthetic stucco such as Exterior Insulation and Finish Systems (EIFS) to avoid moisture intrusion and entrapment against the structure.
- Never cover genuine stucco siding with impermeable paint. It is designed to breathe and release trapped moisture.
- Ensure gutters and down spouts are properly installed and that leaders slope away from the structure.
- Make certain there is positive drainage away from all foundations.
- Install sump pumps in areas having high ground water tables.
- Design landscape to avoid water holding basins and plant or prune shrubs and trees to avoid contact with structure providing clearance for air circulation around the foundation.